News Story
Making Better Makers with New 3-D Printing Technologies
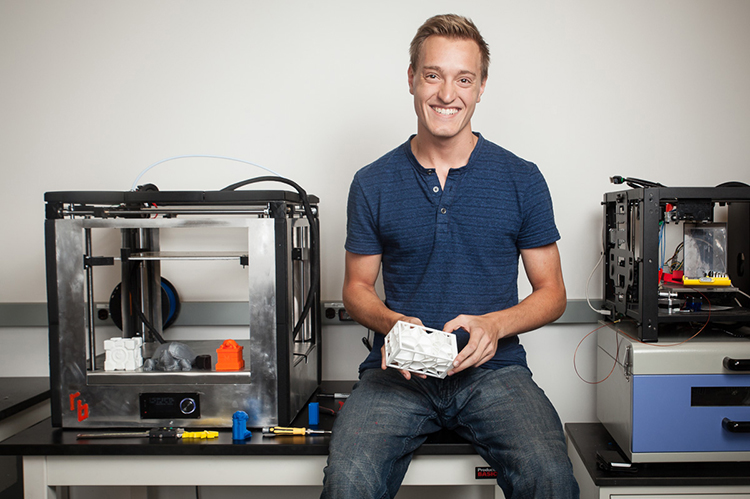
Mechanical engineering senior student Brett Potter set out to fix the most nagging problems of consumer 3-D printers: speed, clogging, and sticky print beds.
After seeing the limitations of popular consumer printers, he created Readybox: a fast, accurate, low-maintenance, reliable 3-D printer with a large print area that he hoped would move the consumer industry forward.
“Readybox addressed the three most important aspects of consumer 3-D printers: generous print area, fast print speed, and high print resolution,” said Craig Dye, director of Maryland Technology Enterprise Institute (Mtech) Ventures and a mentor to Potter. “At the lower end of the market, you could get one of those aspects in a printer. The holy grail was to develop something at a reasonable price point that addressed all three. That is precisely what Potter did.”
Potter started with speed: 3-D prints that take 20 hours on regular 3-D printers would take only three hours with Readybox. Next, he virtually eliminated clogging with a new design that powered through jams. He then forced the system to maintain itself before every print. Lastly, he added a generous print area and a build plate that held prints in place.
“Consumer 3-D printers need to be as fast and as reliable as industrial printers if they are ever truly going to become household items,” said Potter. “I wanted Readybox to be the next step in achieving this goal.”
Potter’s breakthrough innovation with Readybox was a new, patent-pending extrusion system that eliminated clogging and allowed plastic to flow faster than previously possible.
“I figured out a way to spread out the force of the system so it used six points of contact rather than one or two,” said Potter. “This allowed Readybox to apply a crazy amount of pressure to the plastic, pushing it harder and faster so it powered through clogs and improved print speeds.”
To accommodate that speed, Potter added a low friction movement system that allowed Readybox’s print head to move fast while retaining the accuracy of industrial printers. Readybox could print in layer heights from 50 to 450 microns thick, enabling users to choose exactly how much detail they need.
Next was maintenance.
Potter made sure that before every print, Readybox would auto-level its build plate, auto-calibrate, and clean its own nozzle.
He then added a hassle-free, polyetherimide build plate that did not need glue or tape to hold a print in place.
Last was the large print area.
“Readybox’s build volume, 13 inches squared, was something you would see on production-grade machines,” said Anthony Ingelido, Terrapin Works manager. “It meant you could make larger singular items. Overall, the speed to build volume to foot print ratio of the Readybox was really good.”
Last fall, Potter launched a Kickstarter campaign for Readybox, raising $21,284 and exceeding his goal within 24 hours.
He also joined Startup Shell, a student-run coworking space and incubator at the University of Maryland. There he met computer science major Carson Myers, who joined Readybox and proceeded to develop all of the electronics and user interface for Readybox, as well as the company’s website.
“It is great to work with a like-minded person who I can bounce ideas off of and who isn’t afraid to shoot them down,” said Potter.
The team decided to pivot with Readybox and sell the parts that set their printer apart.
“I realized that I am going back to school and not having a large amount of capital to pull from is risky,” said Potter. “By selling parts, our work will also have a greater impact. People can buy our parts, attach them to their printers, and they will perform better.”
To start, Readybox will offer its patent-pending extruder, which prevents jams and pushes harder, allowing the printer to move and print faster, according to Potter.
The company will also offer its print bed or build plate. “Our print bed automatically removes the part, so you print as hard as you want onto the print bed, and it will not take any work to get it off.”
Readybox is slated to release its printer parts this fall. The company plans to have the parts manufactured in the U.S. and assembled in-house.
That assembly will likely occur at the new Startup Village, a house on the edge of the University of Maryland campus created to help bridge the gap for student and alumni entrepreneurs as they grow their business ideas on campus and work toward launching them in the market.
Readybox joined Startup Village as an inaugural member this past summer.
Published October 6, 2016