News Story
"Embedded Cooling" of Next-Generation Power Electronics
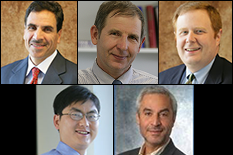
Top: Dr. Michael Ohadi, Dr. Serguei Dessiatoun, & Dr. F. Patrick McCluskey
Bottom: Dr. Bao Yang & Dr. Mehran Mehregany
A University of Maryland (UMD) research team led by Professor Michael Ohadi has won a $2.1 million contract from the Defense Advanced Research Projects Agency (DARPA) to develop "embedded cooling" technology for compound semiconductor microchips and high power electronic systems. The UMD team's efforts, funded by DARPA's ICECool Program, will use an innovative two-phase micro thin film/microfluidics and on-chip thermoelectric coolers to provide an order-of-magnitude improvement in chip cooling rates, while reducing the volume of the cooling package and the amount of the cooling fluid in circulation.
The exponential growth in the capacities and capabilities of computing and electronics technology, known as Moore’s Law, has led to continuous increases in chip computing power and functionality with simultaneous reductions in chip size. This has resulted in an increased on-chip power dissipation density beyond the capability of conventional thermal management techniques. Inadequate cooling has constrained further advances in high performance electronic systems in both commercial and defense applications. This is the motivation for DARPA's IntraChip Enhanced Cooling (ICECool) program that seeks to integrate the thermal management solution directly into the chip layout, substrate structure, and/or package design. This will substantially boost the cooling performance, while introducing significant reduction in the package size, thus allowing higher power densities for the chip.
The Maryland team, composed of Professors Michael Ohadi, Serguei Dessiatoun, Patrick McCluskey, and Bao Yang, will develop a system in which a thin film of fluid is pumped through a series of channels, narrower than the width of a human hair, etched onto the chip's substrate. As the fluid evaporates in a thin film mode, it cools the chip, in the same way the human body uses perspiration for evaporative cooling. When successfully implemented, thin film evaporation can be one of the most effective cooling mechanisms, with potential for at least an order of magnitude higher cooling rates when compared to most of the conventional cooling technologies.
The goal of the project is to dissipate heat at a rate of one kilowatt per square centimeter (1 kW/cm2) across the chip surface and five kilowatts per square centimeter (5 kW/cm2) from sub-millimeter hot spots on the chip. Such cooling demands are representative of the needs of future generations of high-performance integrated circuits utilized in a diverse range of military power electronics and computational electronics.
"With a direct or embedded cooling system, it is possible to achieve high levels of cooling while shrinking the dimensions of the thermal management hardware, since the embedded microfluidic-based system will deliver the cooling in close proximity to the on-chip heat source," said Michael Ohadi, a professor in the mechanical engineering department and the principal investigator of the project. "Each of the topics we are pursuing is at the frontier of the specific technology area and will require pushing the envelope into uncharted territories."
Some of the major challenges that the team faces are designing for material and fabrication constraints, selecting a working fluid that is compatible with military systems, avoiding local dryout, raising the critical heat flux, and ensuring that the system performs reliably under harsh conditions and repeated on-off cycles.
Professor Patrick McCluskey will examine reliability issues, develop physics of failure models, and conduct risk assessment for integrating the new cooling system into the substrate of a microelectronic component. "A crucial aspect of this program is mitigating the degradation of the cooling system and its interconnection with the chip. This is necessary to ensure the device performs reliably over the entire application life cycle," said McCluskey, who is co-principal investigator and will lead the reliability research for implementation of this new technology.
The University of Maryland leads a team involving Case Western Reserve University, Laird Technologies (formerly Nextreme Thermal Solutions), Boeing Space and Intelligence Systems, and Science Research Laboratory in a three-year research program. The collaboration will help ensure that solutions developed will be compatible with defense system requirements.
Co-principal investigator Professor Bao Yang (also of mechanical engineering) will focus on removing heat from hot spots using thermoelectrics. He will collaborate closely with the project’s industrial partner, Dr. Phil Deane at Laird Technologies, to develop the thermoelectric-based hot spot heat removal.
Professor Mehran Mehregany of Case Western Reserve University will develop and optimize the micro-fabrication processes for the chosen silicon carbide substrate and will work in close collaboration with the UMD team in design and fabrication of the cooling modules.
"This is a high-risk, high-reward, disruptive research project," said Ohadi. "Our team is capable of tackling multiple challenges at different physical levels, as part of a single unified research effort. We are confident that our efforts will result in the rapid innovation and development of game-changing technologies that can dramatically alter the future of high heat flux electronic systems."
Maryland's successful ICECool proposal grew out of more than 25 years of research at the cutting edge of thermal packaging technology, with significant funding from industry and government agencies. These efforts were considerably strengthened by Prof. Avram Bar-Cohen, internationally known for his pioneering text books and recently released Encyclopedia of Thermal Packaging, who served as the Chair of Mechanical Engineering from 2001 to 2010. Reflecting the growing need for innovative thermal management techniques, the University of Maryland team is establishing the Maryland Center for Embedded Cooling (MEmCo) to pursue direct cooling in a diverse range of thermal management applications. It is envisioned that MEmCo will directly impact high performance computing, power electronics, renewable energy and smart grid development, energy recovery/conversion, and process intensification applications.
Published May 24, 2013